Airframe:
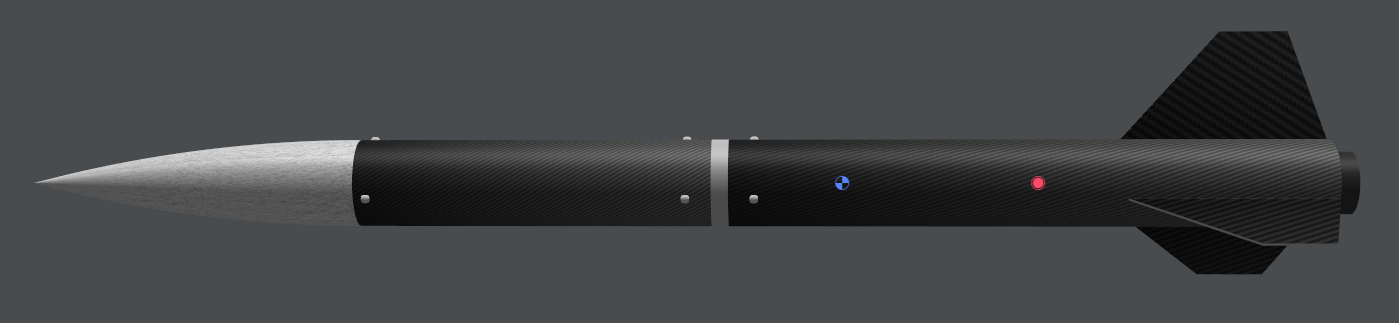
Meridian uses a carbon fiber airframe. This change allows us to increase the rocket body stiffness and allows for a greater inner diameter for components. The body supports all our individual components including our main and drogue parachute, water ballast system, and engine and fin assembly. The inner frame is a combination of polycarbonate carbon fiber 3D printed components and birch wood for weight savings.
The airframe is significantly shorter than our previous design to increase weight efficiency. While this would decrease stability, we have a significantly denser rocket and have redesigned the fins. With these changes we have arrived at a design that is more stable and capable of moving double the payload to 5,000 feet, over double our previous max altitude.
This design utilizes two parachutes, a drogue and main. This allows us to have a back up parachute while also decreasing drift by slowing the rocket’s descent in stages and keeping us closer to our landing zone.